ಕಾರ್ಬೊನೇಟೆಡ್ ಪಾನೀಯ ಉತ್ಪಾದನಾ ಮಾರ್ಗದ ಉಪಕರಣಗಳ ನಿಯೋಜನೆ ಪ್ರಕ್ರಿಯೆಯ ವಿವರಣೆ: ಕಾರ್ಬೊನೇಟೆಡ್ ಪಾನೀಯ ಉತ್ಪಾದನಾ ಮಾರ್ಗವು ಮುಖ್ಯವಾಗಿ ಸಿರಪ್ ಮತ್ತು ನೀರಿನ ಅನುಪಾತವನ್ನು ನಿಯಂತ್ರಿಸುತ್ತದೆ. ಎಲೆಕ್ಟ್ರಿಕ್ ಹೀಟಿಂಗ್ ವಿಧದ ಸಕ್ಕರೆ ಕರಗುವ ಮಡಕೆಯನ್ನು ಹೆಚ್ಚಿನ ಕತ್ತರಿ ತಲೆಯೊಂದಿಗೆ ಅಳವಡಿಸಬಹುದಾಗಿದೆ, ಇದರಿಂದ ಸಕ್ಕರೆ ಕರಗುವ ವೇಗವು ವೇಗವಾಗಿರುತ್ತದೆ ಮತ್ತು ಕರಗಲು ಸುಲಭವಾಗುತ್ತದೆ. ಕಾರ್ಬೊನೇಟೆಡ್ ಪಾನೀಯಗಳ ಮುಖ್ಯ ಘಟಕಗಳು ಸಿರಪ್ ಮತ್ತು ನೀರು, ಮತ್ತು ಅನುಪಾತವನ್ನು ಸುಮಾರು 1: 4 ಮತ್ತು 1: 5 ನಲ್ಲಿ ನಿಯಂತ್ರಿಸಬಹುದು. ಘಟಕಾಂಶದ ತೊಟ್ಟಿಯನ್ನು ಬಿಸಿಮಾಡುವ ಅಗತ್ಯವಿಲ್ಲ, ಮತ್ತು ಸಿರಪ್ ಮತ್ತು ಸಾರದಂತಹ ಸಹಾಯಕ ವಸ್ತುಗಳನ್ನು ಸರಿಹೊಂದಿಸಲಾಗುತ್ತದೆ. ಈ ಸಮಯದಲ್ಲಿ, ತಾಪಮಾನವು ಸುಮಾರು 80 ಡಿಗ್ರಿ. ಪದಾರ್ಥಗಳ ತಾಪಮಾನವನ್ನು ಸುಮಾರು 30 ಡಿಗ್ರಿಗಳಿಗೆ ತಣ್ಣಗಾಗಲು ಕೂಲಿಂಗ್ ವಾಟರ್ ಟವರ್ ಮತ್ತು ಪ್ಲೇಟ್ ಶಾಖ ವಿನಿಮಯಕಾರಕವನ್ನು ಬಳಸುವುದು ಅವಶ್ಯಕ, ತದನಂತರ ತಂಪಾಗುವ ವಸ್ತುವನ್ನು ಪಾನೀಯ ಮಿಕ್ಸರ್ಗೆ ಶುದ್ಧ ನೀರಿನಿಂದ ಮಿಶ್ರಣ ಮಾಡಲು ಕಳುಹಿಸಿ. ಶುದ್ಧ ನೀರಿನಲ್ಲಿ ಆಮ್ಲಜನಕವನ್ನು ಕಡಿಮೆ ಮಾಡಲು ಮಿಶ್ರಣ ಮಾಡುವ ಮೊದಲು ಶುದ್ಧ ನೀರನ್ನು ನಿರ್ವಾತ ಡೀಗ್ಯಾಸ್ ಮಾಡಬೇಕಾಗಿದೆ. ವಿಷಯ.
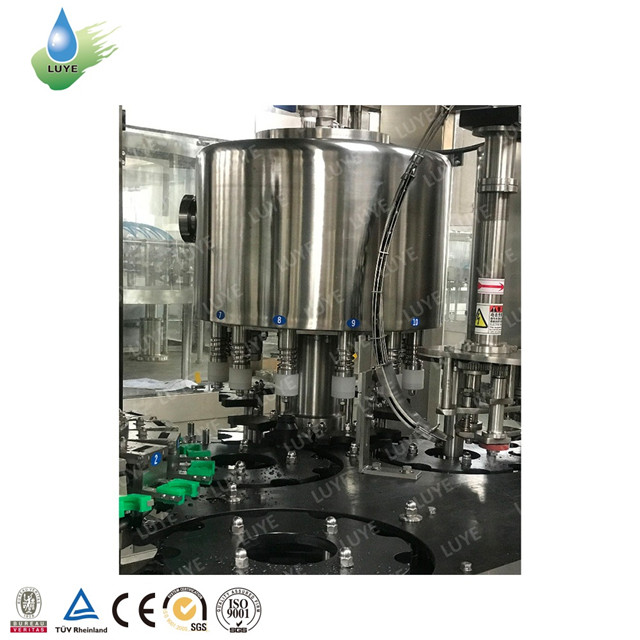
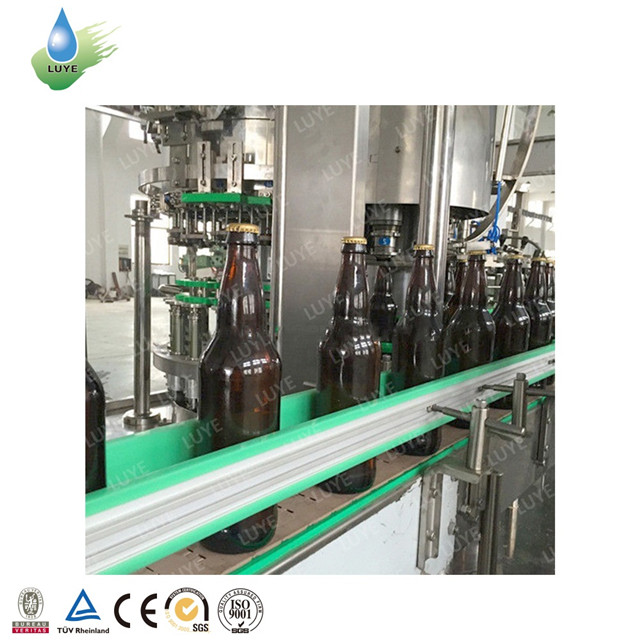
ವಸ್ತುವು ಹೆಚ್ಚು ಇಂಗಾಲದ ಡೈಆಕ್ಸೈಡ್ ಅನ್ನು ಸಂಯೋಜಿಸಬಹುದೇ ಎಂಬುದು ಮುಖ್ಯವಾಗಿ ಈ ಕೆಳಗಿನ ಅಂಶಗಳ ಮೇಲೆ ಅವಲಂಬಿತವಾಗಿದೆ ಎಂದು ನಾನು ಒತ್ತಿಹೇಳಲು ಬಯಸುತ್ತೇನೆ: ವಸ್ತುವಿನ ತಾಪಮಾನ, ವಸ್ತುವಿನ ಆಮ್ಲಜನಕೀಕರಣದ ಮಟ್ಟ ಮತ್ತು ವಸ್ತು ಮತ್ತು ಇಂಗಾಲದ ಡೈಆಕ್ಸೈಡ್ ಮಿಶ್ರಣದ ಒತ್ತಡ. ತಾಪಮಾನ ನಿಯಂತ್ರಣಕ್ಕಾಗಿ, ನಾವು ಚಿಲ್ಲರ್ ಮತ್ತು ಪ್ಲೇಟ್ ಶಾಖ ವಿನಿಮಯಕಾರಕವನ್ನು ಕಾನ್ಫಿಗರ್ ಮಾಡಬೇಕಾಗುತ್ತದೆ. ಮಂದಗೊಳಿಸಿದ ನೀರನ್ನು ಒದಗಿಸಲು ಚಿಲ್ಲರ್ ಅನ್ನು ಬಳಸಲಾಗುತ್ತದೆ, ಮತ್ತು ವಸ್ತು ಮತ್ತು ತಣ್ಣೀರು ಪ್ಲೇಟ್ ಶಾಖ ವಿನಿಮಯಕಾರಕದ ಮೂಲಕ ಶಾಖವನ್ನು ವಿನಿಮಯ ಮಾಡಿಕೊಳ್ಳುತ್ತದೆ ಮತ್ತು ವಸ್ತುವಿನ ತಾಪಮಾನವನ್ನು ಸುಮಾರು 0-3 ಡಿಗ್ರಿಗಳಲ್ಲಿ ನಿಯಂತ್ರಿಸುತ್ತದೆ. ಈ ಸಮಯದಲ್ಲಿ, ಇದು ಇಂಗಾಲದ ಡೈಆಕ್ಸೈಡ್ ಮಿಶ್ರಣ ಟ್ಯಾಂಕ್ ಅನ್ನು ಪ್ರವೇಶಿಸುತ್ತದೆ, ಇದು ಇಂಗಾಲದ ಡೈಆಕ್ಸೈಡ್ಗೆ ಉತ್ತಮ ಸಮ್ಮಿಳನ ವಾತಾವರಣವನ್ನು ಒದಗಿಸುತ್ತದೆ. ಸೋಡಾ ಪಾನೀಯಗಳನ್ನು ಈ ರೀತಿಯಲ್ಲಿ ಉತ್ಪಾದಿಸಲಾಗುತ್ತದೆ.
ಕಾರ್ಬೊನೇಟೆಡ್ ಪಾನೀಯ ಉತ್ಪಾದನಾ ಮಾರ್ಗದ ಭರ್ತಿ ಪರಿಚಯ:
ಕಾರ್ಬೊನೇಟೆಡ್ ಪಾನೀಯ ಮಿಶ್ರಣ ಟ್ಯಾಂಕ್ನಲ್ಲಿನ ಒತ್ತಡವು ಭರ್ತಿ ಮಾಡುವ ಯಂತ್ರದ ದ್ರವ ಸಿಲಿಂಡರ್ನೊಳಗಿನ ಒತ್ತಡಕ್ಕಿಂತ ಹೆಚ್ಚಾಗಿರುತ್ತದೆ. ದ್ರವವನ್ನು ಚುಚ್ಚಲಾಗಿದೆಯೇ ಎಂಬುದನ್ನು ನಿಯಂತ್ರಿಸಲು ಸಾಧನವನ್ನು ನಿಯಂತ್ರಿಸಿ. ಗಾಜಿನ ಬಾಟಲ್ ಕಾರ್ಬೊನೇಟೆಡ್ ಪಾನೀಯ ಭರ್ತಿ ಮಾಡುವ ಯಂತ್ರವು ಮೂರು ಕಾರ್ಯಗಳನ್ನು ಒಳಗೊಂಡಿದೆ: ಬಾಟಲ್ ತೊಳೆಯುವುದು, ಭರ್ತಿ ಮಾಡುವುದು ಮತ್ತು ಮುಚ್ಚುವುದು. ಮರುಬಳಕೆಯ ಗಾಜಿನ ಬಾಟಲಿಗಳನ್ನು ಸೋಂಕುರಹಿತಗೊಳಿಸಬೇಕು ಮತ್ತು ಸ್ವಚ್ಛಗೊಳಿಸಬೇಕು. ಸಣ್ಣ ಉತ್ಪಾದನಾ ಸಂಪುಟಗಳನ್ನು ನೆನೆಸಿ, ಕ್ರಿಮಿನಾಶಕ ಮತ್ತು ಕೈಯಾರೆ ಸ್ವಚ್ಛಗೊಳಿಸಬಹುದು. ದೊಡ್ಡ ಉತ್ಪಾದನಾ ಪರಿಮಾಣಗಳಿಗೆ ಸಂಪೂರ್ಣ ಸ್ವಯಂಚಾಲಿತ ಗಾಜಿನ ಬಾಟಲ್ ಸ್ವಚ್ಛಗೊಳಿಸುವ ಉಪಕರಣಗಳ ಅಗತ್ಯವಿರುತ್ತದೆ. ಸ್ವಚ್ಛಗೊಳಿಸಿದ ಖಾಲಿ ಬಾಟಲಿಗಳನ್ನು ಕನ್ವೇಯರ್ ಚೈನ್ ಪ್ಲೇಟ್ ಯಂತ್ರದ ಮೂಲಕ ತ್ರೀ-ಇನ್-ಒನ್ ಐಸೊಬಾರಿಕ್ ಫಿಲ್ಲಿಂಗ್ಗೆ ಕಳುಹಿಸಲಾಗುತ್ತದೆ.
ಇದು ಐಸೊಬಾರಿಕ್ ಭರ್ತಿ ಪ್ರಕ್ರಿಯೆಯನ್ನು ಹೊಂದಿದೆ. ಮೊದಲನೆಯದಾಗಿ, ಬಾಟಲಿಯ ಒಳಭಾಗವು ಉಬ್ಬಿಕೊಳ್ಳುತ್ತದೆ. ಬಾಟಲಿಯಲ್ಲಿನ ಅನಿಲ ಒತ್ತಡವು ದ್ರವ ಸಿಲಿಂಡರ್ನೊಂದಿಗೆ ಸ್ಥಿರವಾದಾಗ, ಭರ್ತಿ ಮಾಡುವ ಕವಾಟವನ್ನು ತೆರೆಯಲಾಗುತ್ತದೆ ಮತ್ತು ತುಂಬುವಿಕೆಯನ್ನು ಪ್ರಾರಂಭಿಸಲಾಗುತ್ತದೆ. ಇದು ಬಾಟಲಿಯ ಕೆಳಭಾಗಕ್ಕೆ ನಿಧಾನವಾಗಿ ಹರಿಯುತ್ತದೆ, ಇದರಿಂದ ಅದು ಫೋಮ್ ಅನ್ನು ಬೆರೆಸುವುದಿಲ್ಲ, ಆದ್ದರಿಂದ ತುಂಬುವ ವೇಗವು ತುಂಬಾ ನಿಧಾನವಾಗಿರುತ್ತದೆ. ಆದ್ದರಿಂದ, ನಿಜವಾಗಿಯೂ ಉತ್ತಮವಾದ ಐಸೊಬಾರಿಕ್ ಭರ್ತಿ ಮಾಡುವ ಯಂತ್ರವು ವೇಗದ ತುಂಬುವ ವೇಗವನ್ನು ಹೊಂದಿರಬೇಕು ಮತ್ತು ಫೋಮ್ ಅನ್ನು ಹೊಂದಿರಬಾರದು, ಇದನ್ನು ತಾಂತ್ರಿಕ ಶಕ್ತಿ ಎಂದು ಕರೆಯಲಾಗುತ್ತದೆ. ಬಾಟಲಿಯ ಬಾಯಿಯನ್ನು ಭರ್ತಿ ಮಾಡುವ ಕವಾಟದ ಬಾಯಿಯಿಂದ ಬೇರ್ಪಡಿಸುವ ಮೊದಲು, ಬಾಟಲಿಯ ಬಾಯಿಯಲ್ಲಿ ಹೆಚ್ಚಿನ ಒತ್ತಡವನ್ನು ಬಿಡುಗಡೆ ಮಾಡಿ, ಇಲ್ಲದಿದ್ದರೆ ಬಾಟಲಿಯಲ್ಲಿರುವ ವಸ್ತುವನ್ನು ಸಿಂಪಡಿಸಲಾಗುತ್ತದೆ.
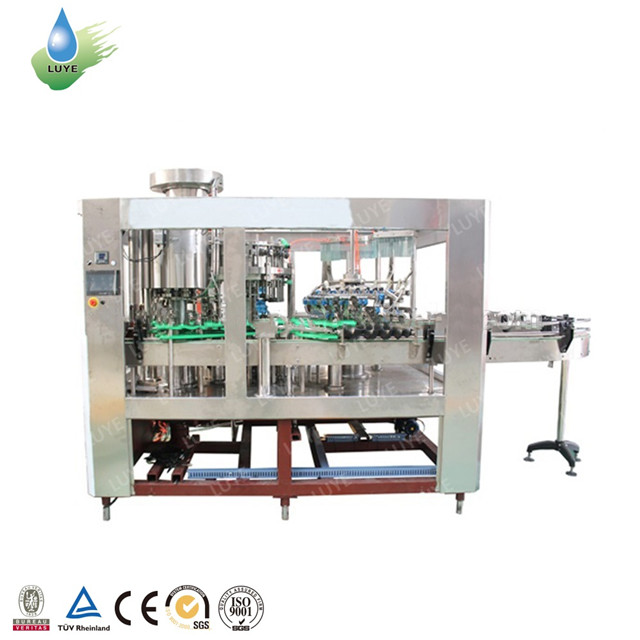
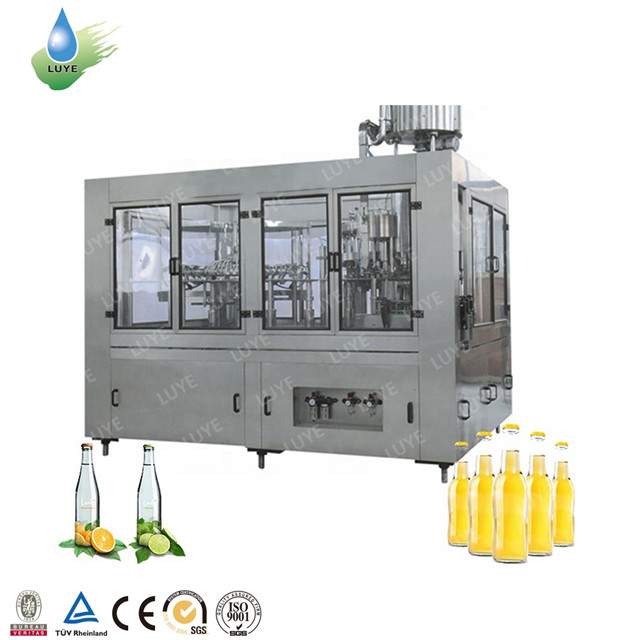